Industry Partner News

Cosmetic Container OEM Chooses CHIMEI’s SAN For Reliably High-Quality Aesthetic
A global cosmetics container original equipment manufacturer (OEM) wanted to expand its market share among top-tier fashion brands. But it was stuck on a quality issue. The OEM uses acrylonitrile styrene (SAN) as its input material, due to its lower cost and higher safety than glass. However, SAN can exhibit unpredictable visual defects, in the form of flash lines appearing on the end-product’s surface. High-end brands and consumers have high aesthetic standards, meaning they will reject any products with visible defects. Facing this barrier to attracting more high-end customers, the OEM approached us at CHIMEI to find a solution to the problem with SAN.
There’s No Data For Aesthetics
While our polymers had already achieved high transparency standards, no one in the industry at that time knew how to predict, let alone prevent the flash lines that could appear in the finished product. Determined to help the OEM, we undertook a major overhaul of our production process. As there were no specific data points that could help track the appearance of flash lines in each batch of SAN, we had to work very closely with our customer. We altered our production process and physically looked at different batches of SAN daily, to identify which temperatures, timings, and ratios produced which visible characteristics. Gradually, we learnt how to assess and track the overall aesthetic quality of the SAN, by understanding what made the flash lines appear.
We found that the batches with the best optical properties, and least flash lines, are produced within a certain time period after our machines’ routine cleaning. Yet, shutting down and cleaning the equipment more frequently would create major inefficiencies, as well as significant waste water. In fact, it isn’t necessary at all. Through the trial-and-error discovery process, we had developed the expertise to determine which specific batches of SAN would not have the undesirable flash lines. That means we can now identify and earmark the batches of SAN with the best aesthetic quality from our normal process cycle, and set those batches aside specifically for the cosmetic container OEM.
Lower Costs, Less Waste, New Markets
This approach has significantly reduced costs and improved efficiencies for our customer. They no longer have to test each batch of incoming SAN. At the same time, their end-product yield rates have improved, thanks to the consistent supply of higher-quality input materials. What’s more, our customer’s market share has grown among higher-end clients, who seek out the OEM’s reliably high-quality containers.
“All quality control people need numbers, criteria and levels… But that wasn’t possible with this request. We ourselves learnt how to screen the quality in a reasonable and workable way to fulfill the customer’s request.”
Wayne Lin
General Plastics Department Manager at CHIMEI
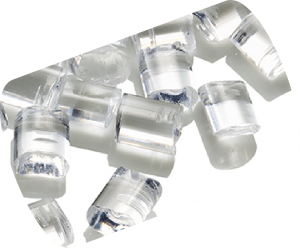
KIBISAN PN-107 L125
Low Residual Monomer SAN
When 100% Transparent Isn’t Enough
SAN offers high transparency, but before our research, no one knew how to prevent the flash lines that would sometimes appear in the finished product. When holding a cosmetics container with a thick transparent wall, that distortion is more likely, diminishing the overall aesthetic appeal of the end-product. High-end brands tend to prefer heavy, and so thick-walled, containers, to give an impression of luxury. Through Client-Side Innovation™, CHIMEI found a way to achieve the luxury feel, without the visual distortion.
refer : www.chimeicorp.com